Compressed air systems consume a significant portion of the electricity used by manufacturing plants. A compressed air audit can identify inefficient compressed air systems that need to be addressed in order to achieve reliable product quality, reduce energy consumption and improve productivity. Compressed air quality is an important part of an audit. Poor air quality adversely affects overall plant operations.
Two primary considerations guide your air requirements. First, what is the air quality needed to meet the product production requirements? Second, what air quality controls are needed to ensure that the air being produced doesn’t pickup or create problems within the compressed air system? For example, if the compressed air isn’t dried after being compressed, it often will create condensed water in the plant air system. This is because the air is hot after being compressed and can hold more moisture than when it cools down.
So what you want is air that is clean and dry and appropriate to your production needs. That requires understanding your facility’s true needs and uses, and it also requires maintaining the filters, separators and driers essential to proper compressed air system performance.
UNDERSTANDING YOUR FACILITY
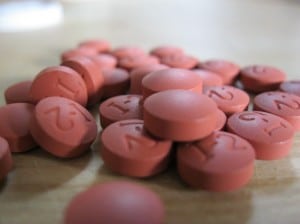
Direct Product Contact, Indirect Product Contact, USP and ISO 8573 air guidelines and standards are common sources from which site-specific air quality specs are developed. They influence compressed air usage in pharmaceutical, medical device, food/beverage, and other manufacturing operations.
In the absence of specified standards governing compressed air quality testing in the manufacturing process or production of pharmaceutical, medical device, and food/beverage applications, it is often best to use composite, site-specific testing programs. This may be the most assured way to produce valid, repeatable testing results that will reinforce your site’s quality. Direct Product Contact, Indirect Product Contact, USP and ISO 8573 air guidelines and standards are common sources from which to draw. A routine testing schedule for your compressed air quality program should provide the appropriate verification and compliance each facility will need for OSHA, FDA and cGMP.
It is imperative that you understand the real needs of each site. You do not need to expend the time and money to establish a quality of air that you don’t actually need. “Clean room” air in a non-clean room air operation, for example, is unnecessary. Specifying air to that level requires expensive equipment to clean and maintain it.
If you bring clean room-class level air into a non-clean room environment the quality of the clean air is decreased to the level of the room environment. You’ve brought a small amount of clean air into a larger volume of air at a lower level; and the money spent on clean and testing that air to ensure it stays clean has probably been wasted.
TRI Air Testing provides independent laboratory support for many manufacturing companies. When these companies’ plant engineers assess and identify the right air quality tests for compliance, operational efficiency, and safety, they collect samples with equipment and media provided by TRI. The samples are submitted to TRI’s lab for analysis, and reports are available within 24 hours. Contaminants to test for include oil, particulate, moisture, and mold/bacteria.
MANUFACTURING OPERATIONS
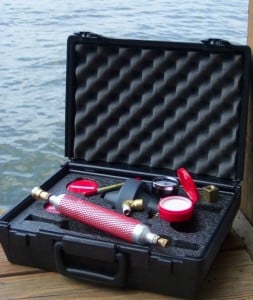
Sampling kits such as this one allow plant engineers to capture air quality samples for quick turnaround of reports from TRI Air Testing’s independent laboratory.
Facilities with clean room needs, such as those handling implantable devices (e.g., knee and hip joints, defibrillators and pacemakers) cannot have particulate matter on their surface affecting the safety of product. These facilities must utilize a spec that ensures a heightened level of particle control.
But for operations that might be using compressed air to blow out bottles before putting in tablets or simply running a piece of machinery, that most stringent air standard may be excessive. It may lead to greater operational expense or present the facility with a test that is difficult, if not impossible to pass—and all on a process that does not actually need that high of a quality of air.
If only 1% of a facility, for example, uses a very high-quality air for a specific application, but the general air use in the rest of the facility does not need that quality of air, a point-of-use filter may be the right solution and help achieve greater operational efficiency.
Understanding the real impact of air quality on the specific zone of work, the people performing the work, and the product being produced or serviced will go a long way towards guaranteeing compliance, levels of safety and the quality the FDA and other regulatory entities want to see.
QUALITY
Check the accreditations and quality policy of the laboratory you choose for compressed air quality testing. For example, do they have a quality system in compliance with ISO/IEC 17025 General Requirements for the Competence of Testing and Calibration Laboratories and with ANSI/ISO/ASQ 9001-2000 Quality Management Systems Requirements?
The quality of the independent laboratory you use is vital to ensuring that your facility’s efforts to achieve energy-efficient, safe air practices (for personnel and product health) are optimized.
Understanding your true compressed air quality needs and utilizing high-quality laboratory support are keys to air quality compliance in manufacturing.